Synthetic silica, also known as amorphous silica, is a versatile and widely used material with diverse applications across various industries. It is a synthetic form of silicon dioxide (SiO2) that lacks a crystalline structure. This article provides a comprehensive overview of synthetic silica, including its properties, applications, and production methods.
Properties of Synthetic Silica:
1. Amorphous Structure: Unlike crystalline silica, synthetic silica lacks a regular internal arrangement of atoms. This amorphous structure gives it unique properties and enhances its suitability for numerous applications.
2. High Purity: Synthetic silica is available in high-purity forms, typically exceeding 99% SiO2 content. This purity ensures its chemical stability and makes it suitable for demanding applications.
3. Porosity: Synthetic silica can be engineered to possess controlled porosity, allowing for specific absorption, adsorption, and catalytic properties.
4. Thermal Stability: It exhibits excellent thermal stability, retaining its properties at high temperatures, making it suitable for applications requiring heat resistance.
5. Low Density: Synthetic silica is a lightweight material, offering a favorable strength-to-weight ratio and making it suitable for applications where weight reduction is desired.
Applications of Synthetic Silica:
1. Fillers and Reinforcements: Synthetic silica is extensively used as a filler or reinforcing agent in rubber, plastics, paints, adhesives, and composites. It enhances mechanical properties, improves dimensional stability, and increases resistance to abrasion.
2. Catalysts and Adsorbents: The unique porosity of synthetic silica makes it valuable in catalytic reactions and as adsorbents. It finds applications in the production of chemicals, petroleum refining, and environmental remediation.
3. Pharmaceutical and Cosmetic Industry: Synthetic silica is commonly used in pharmaceuticals as an excipient, facilitating drug delivery and stability. In cosmetics, it serves as an anti-caking agent, absorbent, and thickening agent in various products.
4. Food and Beverage Industry: Synthetic silica is approved for use in the food and beverage industry as an anticaking agent, clarifying agent, and carrier for flavors and nutrients. It improves flow properties, prevents clumping, and enhances product stability.
5. Electronic and Electrical Components: Due to its excellent electrical insulating properties, synthetic silica is used in the production of circuit boards, electronic encapsulation, and insulating materials.
6. Refractories and Ceramics: Synthetic silica is utilized in the manufacturing of refractories, ceramics, and glass products due to its high-temperature stability, low thermal expansion, and resistance to chemical corrosion.
Production Methods:
1. Precipitation Method: In this method, a silica precursor such as sodium silicate or silicic acid is mixed with a mineral acid, resulting in the precipitation of amorphous silica. The obtained precipitate is then washed, dried, and milled to obtain the desired particle size.
2. Sol-Gel Method: The sol-gel process involves hydrolysis and condensation of silicon alkoxides, such as tetraethyl orthosilicate (TEOS), in the presence of a solvent and a catalyst. This method allows precise control over the composition, structure, and porosity of the resulting silica.
3. Flame Hydrolysis Method: In this technique, silicon tetrachloride vapor is introduced into a high-temperature flame, where it reacts with oxygen to form fine particles of amorphous silica. The particles are then collected, purified, and subjected to further processing as required.
Conclusion: Synthetic silica, with its unique properties, has become an indispensable material across numerous industries. Its versatility, thermal stability, and controlled porosity make it suitable for a wide range of applications, including fillers and reinforcements, catalysts and adsorbents, pharmaceuticals, cosmetics, food and beverages, electronic and electrical components, as well as refractories and ceramics. The production of synthetic silica involves methods such as precipitation, sol-gel, and flame hydrolysis, enabling the customization of its properties for specific applications.
In the field of fillers and reinforcements, synthetic silica is widely used to enhance the mechanical properties of various materials. When incorporated into rubber or plastics, it improves strength, flexibility, and resistance to abrasion. In paints, adhesives, and composites, synthetic silica acts as a filler, improving dimensional stability and imparting desirable properties to the end product.
The unique porosity of synthetic silica makes it valuable as catalysts and adsorbents. In catalytic reactions, the large surface area and controlled porosity of synthetic silica provide an ideal environment for chemical reactions to occur. It finds applications in industries such as petroleum refining, where it acts as a catalyst support, facilitating efficient and selective reactions. Additionally, synthetic silica’s adsorption capabilities make it useful for environmental remediation and purification processes.
Synthetic silica plays a crucial role in the pharmaceutical and cosmetic industries. In pharmaceuticals, it is commonly used as an excipient, aiding in drug delivery, stability, and dissolution. Synthetic silica’s porous structure allows it to act as a carrier for active ingredients, enhancing their bioavailability. In cosmetics, it serves as an anti-caking agent, absorbent, and thickening agent, improving the texture and performance of various personal care products.
The food and beverage industry extensively employs synthetic silica as an approved food additive. It acts as an anticaking agent, preventing clumping or sticking of powdered food products. Additionally, synthetic silica serves as a clarifying agent, removing impurities from beverages such as beer and wine. It is also used as a carrier for flavors, nutrients, and food colorants, ensuring their uniform dispersion and stability.
In the electronics and electrical industry, synthetic silica’s excellent electrical insulating properties make it indispensable. It is used in the production of circuit boards, where it provides insulation between conductive layers and components. Synthetic silica is also utilized in electronic encapsulation, protecting delicate components from moisture, dust, and mechanical stress. Its thermal stability ensures reliable performance even at elevated temperatures.
Refractories, ceramics, and glass manufacturing heavily rely on synthetic silica. Its high-temperature stability, low thermal expansion, and resistance to chemical corrosion make it an essential component in these industries. Synthetic silica is used in the production of refractory materials, which withstand high temperatures in furnaces and kilns. It is also employed in ceramic compositions, contributing to their strength, stability, and resistance to thermal shock. In glass production, synthetic silica acts as a flux, reducing melting temperatures and enhancing the transparency and durability of the final product.
In conclusion, synthetic silica is a versatile material with a wide range of applications across numerous industries. Its properties, including amorphous structure, high purity, controlled porosity, thermal stability, and low density, make it suitable for diverse uses. From fillers and reinforcements to catalysts, pharmaceuticals, food additives, and electronics, synthetic silica plays a vital role in enhancing the performance and properties of various products. With different production methods available, synthetic silica can be tailored to meet specific requirements, further expanding its potential applications in the future.
Synthetic silica
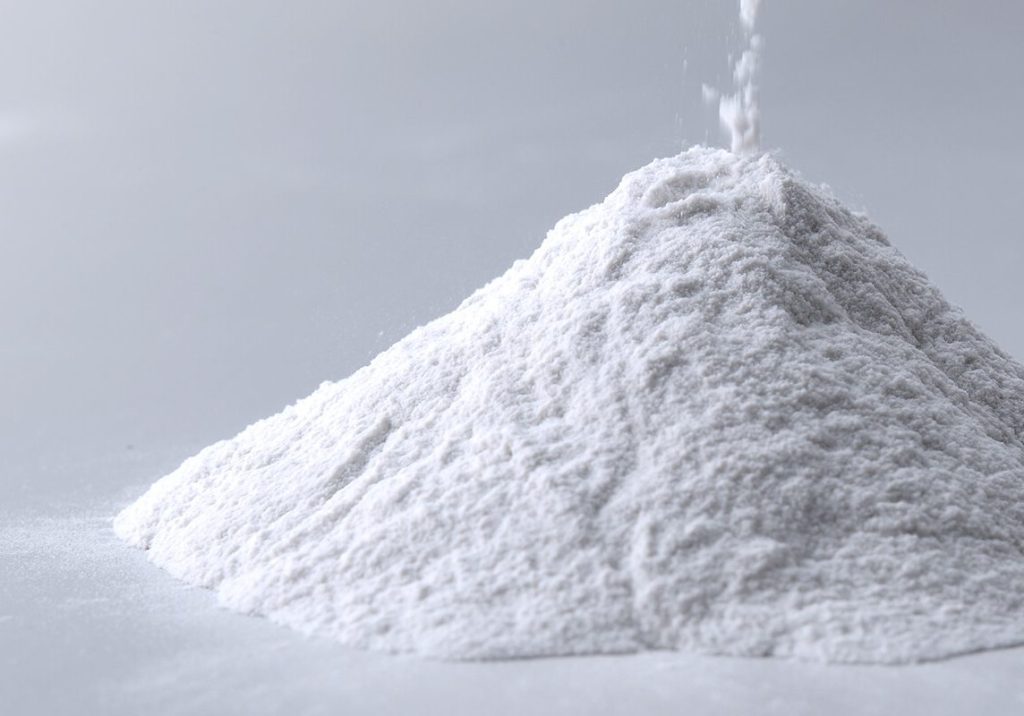